Let’s Talk Fibers – Kevlar
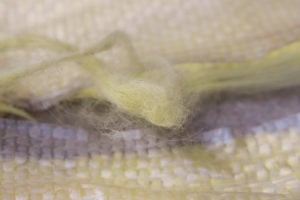
You have certainly heard the expression “all roads lead to Rome,” which originally meant that since Rome was the center for world commerce and logistics, all roads literally did lead to Rome at the height of their empire. Looking at the origins of synthetic fibers used in conveyor belting, the expression “all materials lead to DuPont” would be quite accurate!
Kevlar, our current fiber to discuss, was invented by the chemist Stephanie Kwolek, while she worked for DuPont in 1964. She was an American chemist that was part of a group looking for a new, strong and lightweight fiber to use in tire production. As often happens in early testing, Kevlar was not an instant success- it was usually thrown away in testing as it is was “cloudy, opalescent upon being stirred, and of low viscosity.” Kwolek, who believed that there was something valuable in this product, convinced the technician who ran the spinneret, to test her solution- and they were amazed to find that the Kevlar fiber did not break, like nylon. This was a huge discovery of course, and a whole new field of polymer chemistry was born! Seven years later, in 1971, modern Kevlar was introduced, and the applications for Kevlar developed in the 1980s under Dr. Jacob Lahijani (of DuPont).
WHAT IS KEVLAR?
There are not many belting materials that can double as body armor, so what is Kevlar and how is it so strong? What makes it good for belting? There are 4 key properties to Kevlar. Kevlar has high strength, high modulus, toughness, and thermal stability. One of the issues with nylon and polyester was the fact that they were considered a flexible- chain polymer, which required a “chain disentanglement and orientation” as a solid, which made the tenacity and modulus levels far below what their theoretical value could be. The polymer that developed into Kevlar was a liquid crystalline polymer that allowed the formation of rod-like molecular structures that were not diminished by any alteration of form as a solid. This liquid crystalline polymer, under shear forces when passed through a spinneret, become fully oriented in the direction of the shear. This process is what allows the Kevlar to achieve very strong fibers!
Did you catch all that? We can leave the true chemical understanding of Kevlar up to DuPont, but we can know that because of the closely packed polymer chains in structure, Kevlar is 5 times stronger than steel and able to withstand both fire and bullets.
As far as heat resistance, in DuPont’s own words, “Kevlar® is inherently flame resistant—protecting against thermal hazards up to 800 degrees Fahrenheit. Additionally, Kevlar® fibers won’t melt, drip or support combustion.” There are many different Kevlar variants, listed mostly by numbers following the name, such as Kevlar 29, Kevlar 49, Kevlar 100. Each one of these variants has been tested and formulated for specific industries and applications, such as Kevlar 49 being the variant used in body armor.
KEVLAR AS A PARTNER FABRIC
Kevlar also bonds well with other fabrics in situations where the heat resistance of Kevlar isn’t needed on both sides of the product. As you could imagine just from reading the details in this article, Kevlar is a very expensive material! The aluminum extrusion process is a great place to see where Kevlar and Kevlar combined products are used. If you haven’t checked out INO’s Aluminum Extrusion video, see it here.
KEVLAR BY ANY OTHER NAME
I remember vividly a moment of true embarrassment as a third grader in a small rural New York private school. Nike Air Jordans were still a relatively new phenomenon, and everyone wanted them. I did not really understand the difference between a discount store and an actual shoe store so I was so excited to find what I thought were Nike Air Jordans at K-Mart when I was shopping with my mom. I begged her to buy them, and was shocked when she did! I thought they must be so expensive, but they were most likely around $14.99.
I proudly wore those sneakers the next day to school, and I had my third grade class fooled completely, heck, I was still fooled! My teacher, Mr. Pitcher, announced that he needed a volunteer to run a note to the senior class homeroom teacher, and I was quick to volunteer, as I realized that it was my opportunity to show the coolest kids in school my sneakers.
I casually cruised into that homeroom with the note for the teacher and waited for the response. Things went downhill very quickly as a roar of laughter filled the room. Maybe in my memory I have built up this moment, but I remember a whole group of them pointing and laughing and someone saying, “Look! This kid is wearing Fake Jordans!” I don’t remember if the swoosh was upside down, or if the MJ silhouette was backwards, or what let them know so quickly that I was wearing fakes, but I clearly remember running out of that room and crying all the way back to my classroom, with my bubble completely burst. Those shoes quickly found the bottom of the garbage can.
Why would I tell that story here? Well, there are some alternatives to Kevlar, and some will say that these alternatives are the same as those Fake Jordans. Are they? Kevlar is the registered name from DuPont for the product, which is why there is a little R next to every reference to it. There are other products that have been created after Kevlar that contain the same chemical makeup, and can be used as an alternative. Are they exact? No, but they are a comparable substitute. Kevlar is a para-aramid fiber, sometimes just referred to as Aramid. There are other aramid fibers like Twaron, Technora, Heracron, and Alkex, The main alternative to Kevlar that you will see is Twaron, which was developed a decade after Kevlar, but because of some financial issues within the company, the product didn’t come to market until later in the 1980s.
To take my Fake Jordans application even further, when you buy Kevlar from DuPont, you need to be aware that you can buy either new fiber or recycled fiber. They look identical but the recycled fiber has all of its properties reduced! You might get a quote on a Kevlar belt and be shocked that it seems so much cheaper than the other quotes- but don’t be deceived! that cheap belt is probably an inferior recycled option. Just remember, they don’t sell Air Jordans at Walmart.

INDUSTRY APPLICATIONS – THE YELLOW BELTS
There are many applications with high abrasion and/or high heat where the traditional PU/PVC belting will not suffice. A few of these are aluminum extrusion lines, glass extrusion, and metal forming. The mining industry is another key application for Kevlar belting as it relies on the high abrasion resistance for extracting and transporting tons of ore for processing.
Woven Kevlar belts can be made with steel wire or carbon fibers woven through the carcass of the belt to help dissipate the heat on the conveyor faster. You will typically find these in 2-ply and 4-ply variations.
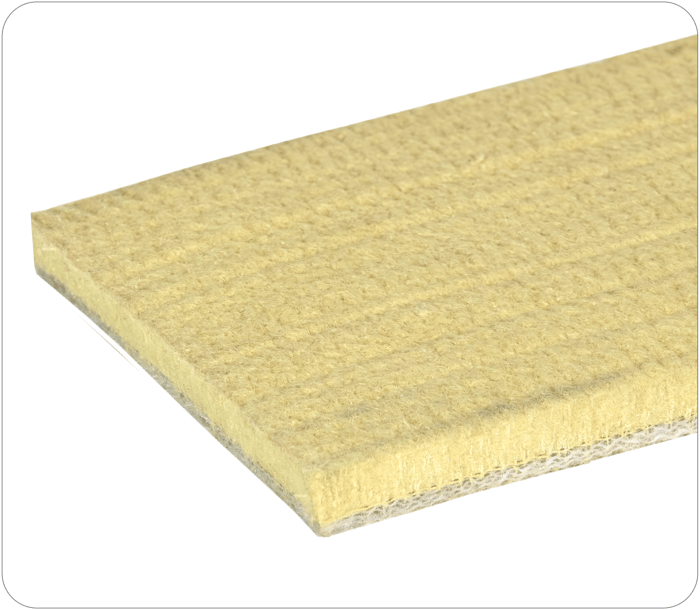
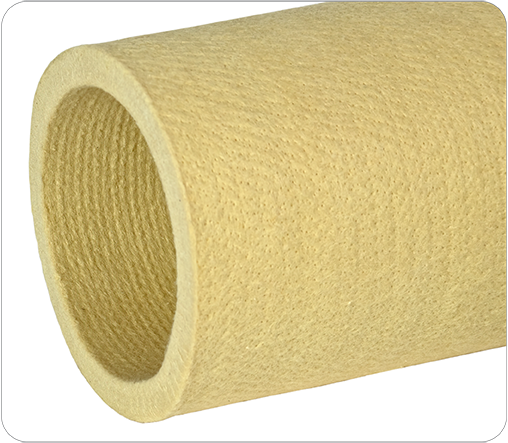
In needled Kevlar belts, you will find belts that can be treated with resin to increase wear and abrasion resistance as well as high density needled Kevlar pads and Kevlar roller covers for those extrusion lines.
Kevlar also has a place in the carcass of lightweight belting! For example, printing blankets TPU belts have a Kevlar ply to increase the strength of the belt. Other applications with Kevlar as a ply of the belt are stackers for the plywood industry or even prepress belts on particle board forming lines where the belts have 50 to 65N/mm pull per 1%.
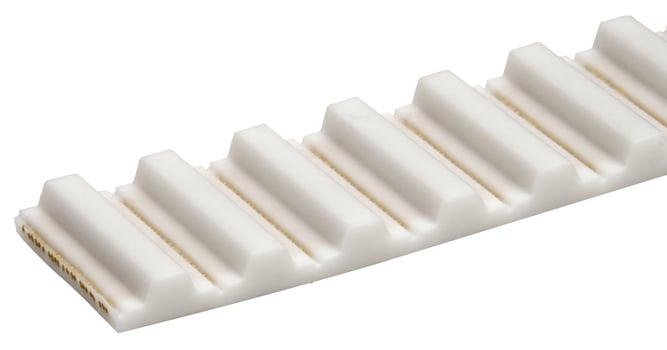
Kevlar is also found in both types of belts used for linear positioning applications- timing and v- belts. These belts have internal tensile cords that serve as the primary load carrying component. Steel is typically the cord material that is used, but Kevlar tensile cords provide better shock and impact resistance than steel or other materials. V-belts with Kevlar tension cords are rated for higher loads than those with other materials.
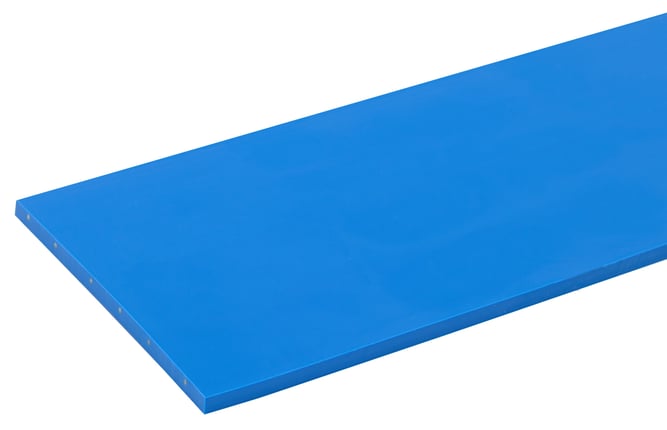
Some companies, like INO and Habasit for example, use Kevlar cords as reinforcement for their homogeneous polyurethane line to reduce elongation.
Kevlar also has a lower stretch than other tensile cord types, so the Kevlar reinforced belts have less elongation over time. This is going to provide a more consistent belt length take-up.
One concern for Kevlar is that in wet or humid environments the Kevlar cords absorb and release moisture causing a change in length. This can affect the performance of the belt.
The other concern of Kevlar is that it has a negative thermal coefficient of expansion- which means it shrinks as the temperature rises and lengthens as it cools which is opposite of most other machine components, so it may not be suitable in an environment with extreme fluctuations- extreme temps are okay, it is the fluctuations that could create issues.
BODY ARMOR SHOULDN’T COME CHEAP!
When you understand the strength and structure of Kevlar, you understand why it comes at a pretty steep cost for conveyor belting, but you do know that you get what you pay for. The strength, endurance, and heat resistance of Kevlar belting makes it the perfect choice for applications that demand exceptional performance. The fact that Kevlar can be bonded with other materials is also a great advantage, as that allows it to be used as a carcass for lightweight conveyor belts.
This article is not focusing on the disadvantages of Kevlar, as it is a material that serves a very specific purpose. But does Kevlar have any shortcomings? It reacts badly to sunlight unless it is protected, and it is difficult to cut and shape in comparison to other materials. It also can suffer some corrosion if exposed to chlorine. Kevlar also tends to absorb moisture, so in applications where high moisture resistance is needed, it would need to be combined with another product.
It is amazing to think that if Stephanie Kwolek hadn’t convinced the technician at DuPont to keep testing the material that became Kevlar, we might not have this amazingly strong and versatile product! She was a true world changer!
LEAVE A REPLY